- Home
- Startup news
- Biosurfactants from food waste? Meet AmphiStar
Biosurfactants from food waste? Meet AmphiStar
Biotope startup AmphiStar has developed a versatile tech platform that can create diverse biosurfactants using nearly any biobased material, including food waste. The startup’s aim is to make sustainable biosurfactants mainstream and aid in the transition from fossil-based to bio-based industry. Discover more in this interview with co-founders Sophie Roelants and Bernd Everaert
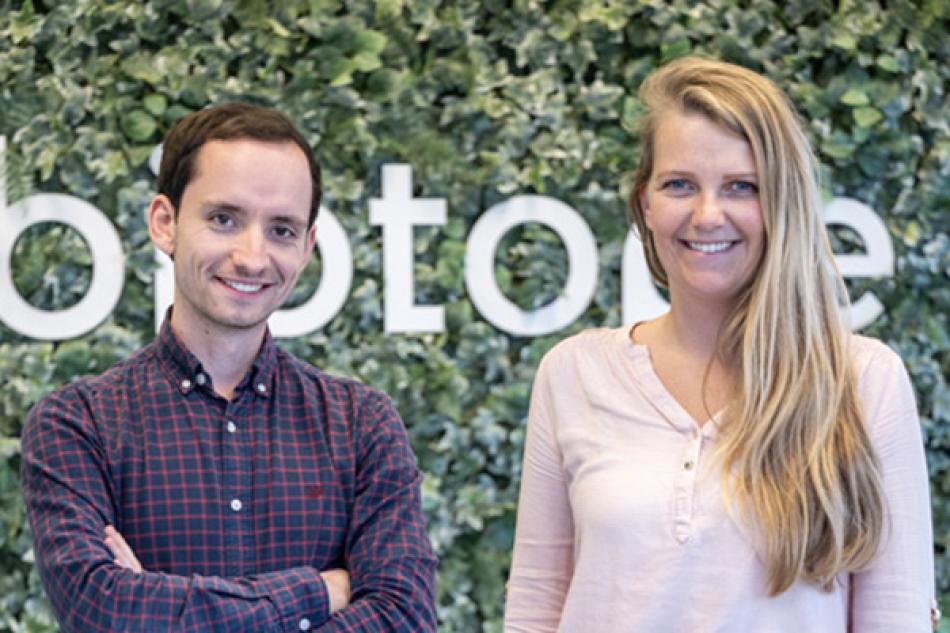
What are surfactants?
Sophie Roelants (Co-Founder and CEO): “Surfactants are ingredients that are found in just about everything we use. When you took a shower or brushed your teeth this morning, your shampoo and toothpaste contained surfactants. They are in your dishwashing liquid, the paint on your house, even the ink in your ballpoint pen.
There’s a huge variety of different types, but essentially they are all composed of amphiphilic molecules that interact with both hydrophilic and hydrophobic substances, like water and oil.”
Bernd Everaert (Co-Founder and CTO): “Surfactants are present in an extensive range of products, making it a huge market. To put it into perspective, the global yearly production volume of surfactants can be compared to all wine bottles found on the shelves of every supermarket worldwide.
The vast majority are made by big chemical companies and are fossil- or palm oil-based biosurfactants –. However, there is a growing push for more sustainable biosurfactants as consumers advocate for more sustainable options.
Currently, only 4% of surfactants are biobased, and less than 0.5% are produced using a biological process, but the momentum for change is increasing in the industry, as shown by clear and ambitious commitments by f.e. Unilever and Evonik.
AmphiStar goes a step further and develops biosurfactant production technologies using food waste from supermarkets, avoiding direct land use for their production.”
Sophie Roelants: “This momentum and push for better options is why Bernd and I launched AmphiStar together with three other co-founders – Wim Soetaert, Karolien Maes, and Sofie De Maeseneire – as a spin-off of the Bio Base Europe Pilot Plant and the University of Ghent (InBio.be).
Using our tech platform, we’re aiming to make biosurfactants mainstream by producing next-generation biosurfactants at an industrial scale from sustainable feedstocks.”
Subscribe
Subscribe for Exclusive Updates and Exciting News!
Thank you
You are subscribed to my newsletterUsing our tech platform, we’re aiming to make biosurfactants mainstream by producing next-generation biosurfactants at an industrial scale from sustainable feedstocks.
Sophie Roelants
What sets your technology apart?
Sophie Roelants: “We have developed a unique proprietary production platform in terms of input, method, and output, making our technology ‘triple-bio’. Firstly, we use sustainable biobased feedstocks as our base input. We can use a range of biobased feedstocks and convert these into a versatile set of biosurfactant molecules, to meet the diverse needs in the surfactant market.
The issue with most biosurfactants today is that they are primarily produced from palm oil using harsh chemical processes relying on toxic catalysts, and high temperatures and pressures. On top of this, palm oil production is associated with environmental issues like deforestation and CO2 emissions from long-distance transportation.
To ensure that our surfactants are truly sustainable, we are instead sourcing our biomass from waste streams and industrial side streams, like discarded food from supermarkets or companies.”
Bernd Everaert: “Secondly, we use a mild biological production process performed in water at low temperatures and pressures. To make sure that our products are green from start to finish, we convert the waste into biosurfactants via a clean, safe, and eco-friendly process with technology that is sustainable even at large scale.
Thirdly, our biosurfactants are biocompatible – biodegradable and safe for both people and environment, even after they’ve washed down the drain.”
How does your process work?
Sophie Roelants: “It’s actually very similar to brewing beer, where you use yeasts to convert sugar into alcohol. In the same way that specific yeasts give you different types of beers, we use specialized microorganisms to convert waste into various types of biosurfactants.
We mainly work with the yeast Starmerella bombicola, originally isolated from bumblebees, where it naturally turns sugar into surfactants. It’s where we got the name AmphiStar: ‘Amphi’ from amphiphilic, and ‘Star’ from Starmerella.
“We’ve expanded the microbes we work with into a whole collection, with modified versions of Starmerella as well as other microorganisms. This wide variety allows different applications – surfactants with specific properties are needed depending on the type of product.
For example, shampoos require different surfactants than paints. We won’t change the world with one molecule; we need a whole catalogue. Additionally, we focus on rapidly producing large volumes, to drive down the costs.
We already demonstrated our capacity to scale up to industrial levels with the large bioreactors at the Bio Base Europe Pilot Plant, and we’ve developed a purification process that efficiently extracts the biosurfactants from the fermentation mix, providing plenty of end product ready to be used by industry partners.”
We will soon launch our first consumer product together with an industry partner: a cleaning spray for surfaces, like in your kitchen. It’s the world’s first product to use 100% waste-based biosurfactants.”
Bernd Everaert
Bernd Everaert: “In terms of tech maturity, we are ready to launch. We seek to partner with large companies developing personal and home care products.
We will soon launch our first consumer product together with an industry partner: a cleaning spray for surfaces, like in your kitchen.
It’s the world’s first product to use 100% waste-based biosurfactants, and we’re very excited to hear what people think of it.
This is AmphiStar’s aim: make biosurfactants mainstream and aid in the transition from fossil-based to bio-based industry and a circular economy.”
More News
AmphiStar secures €12.5m EIC funding
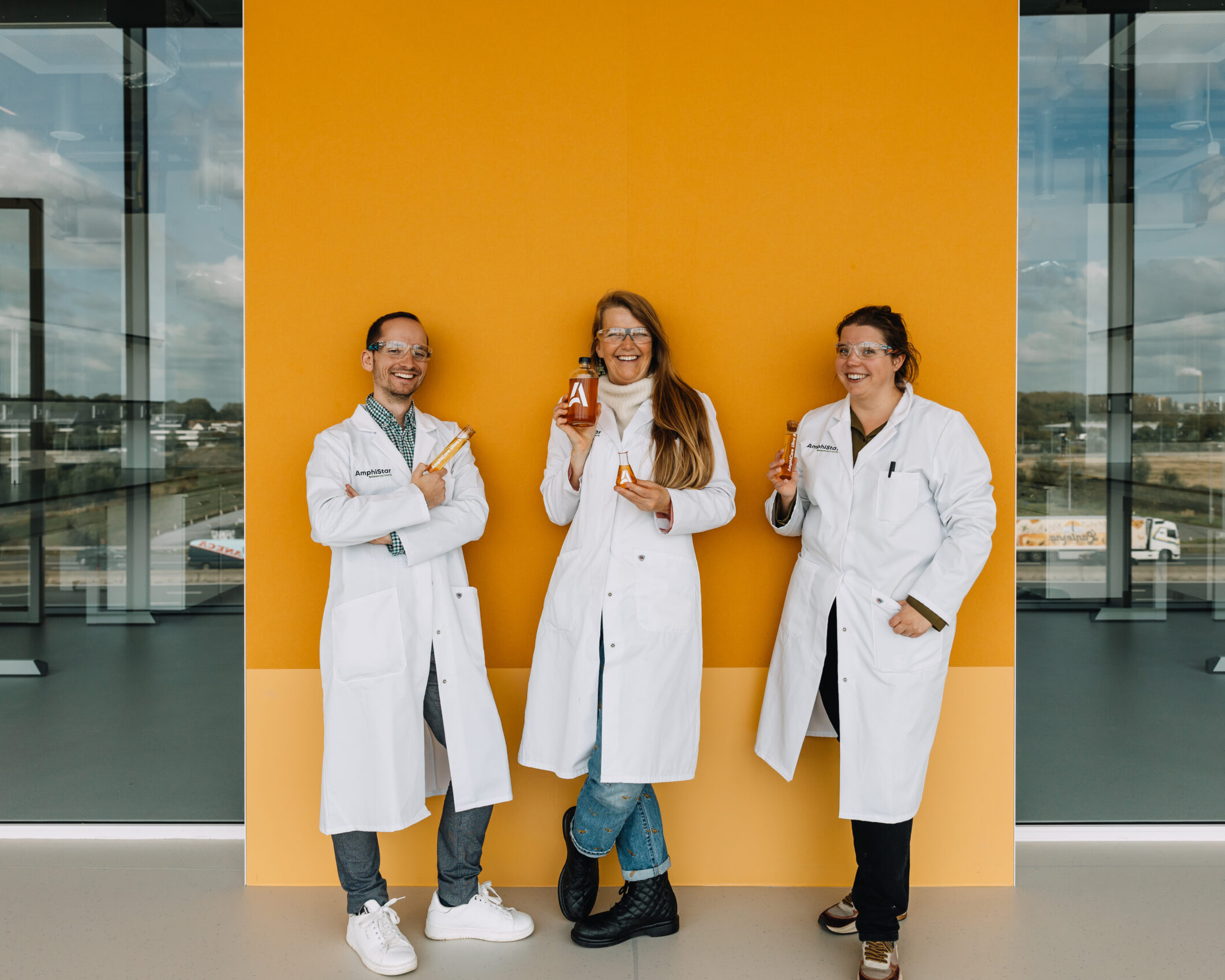
biotope recap: Summer edition
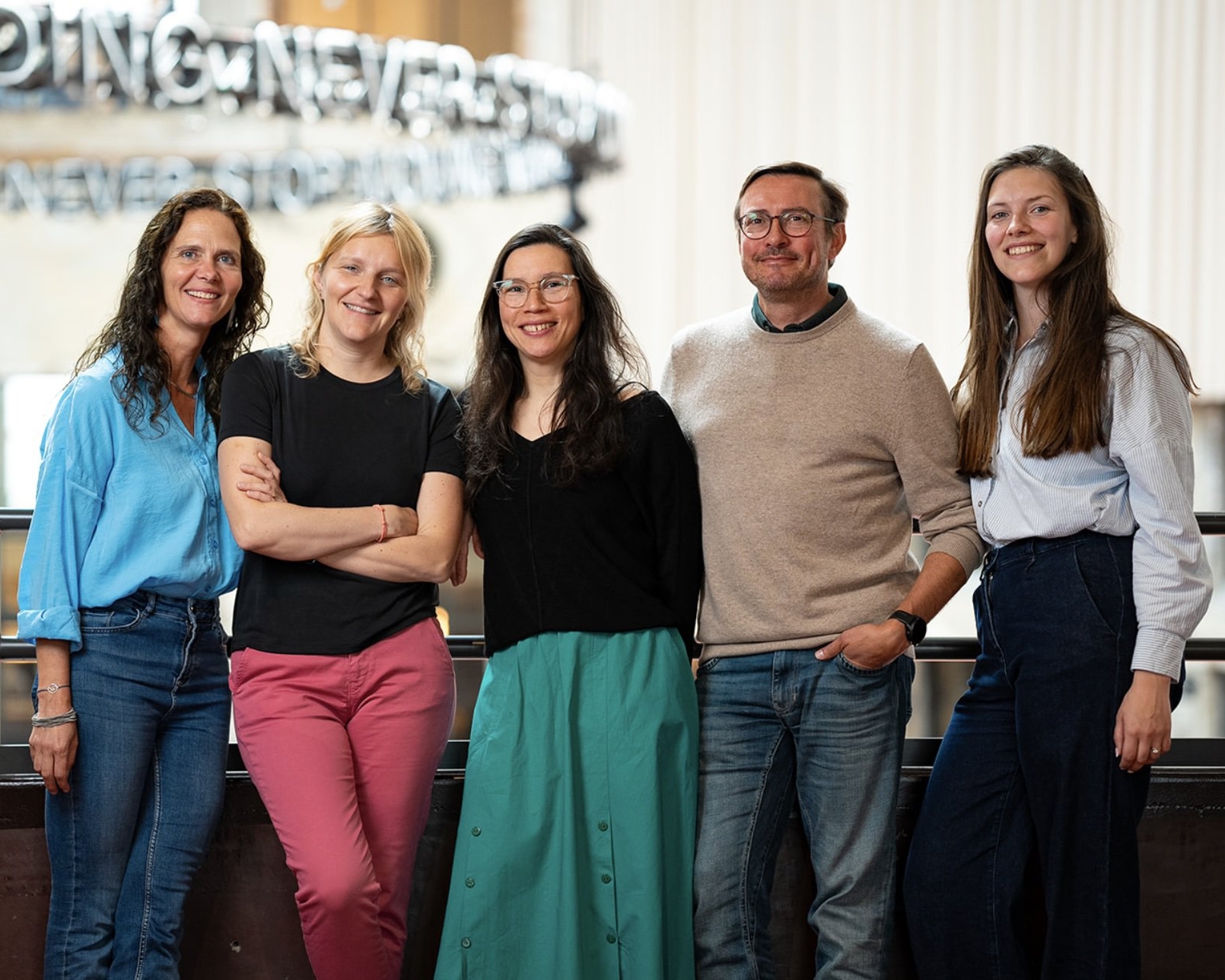
Annick Verween on the VCo2 podcast
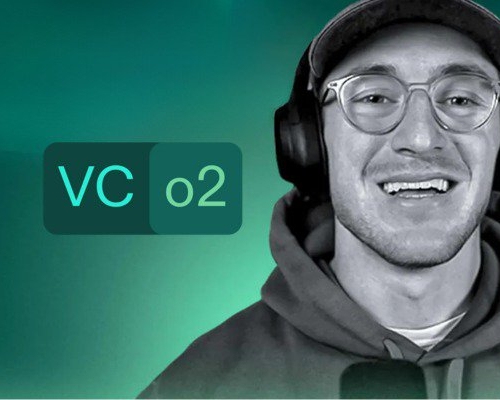
2024 wrapped
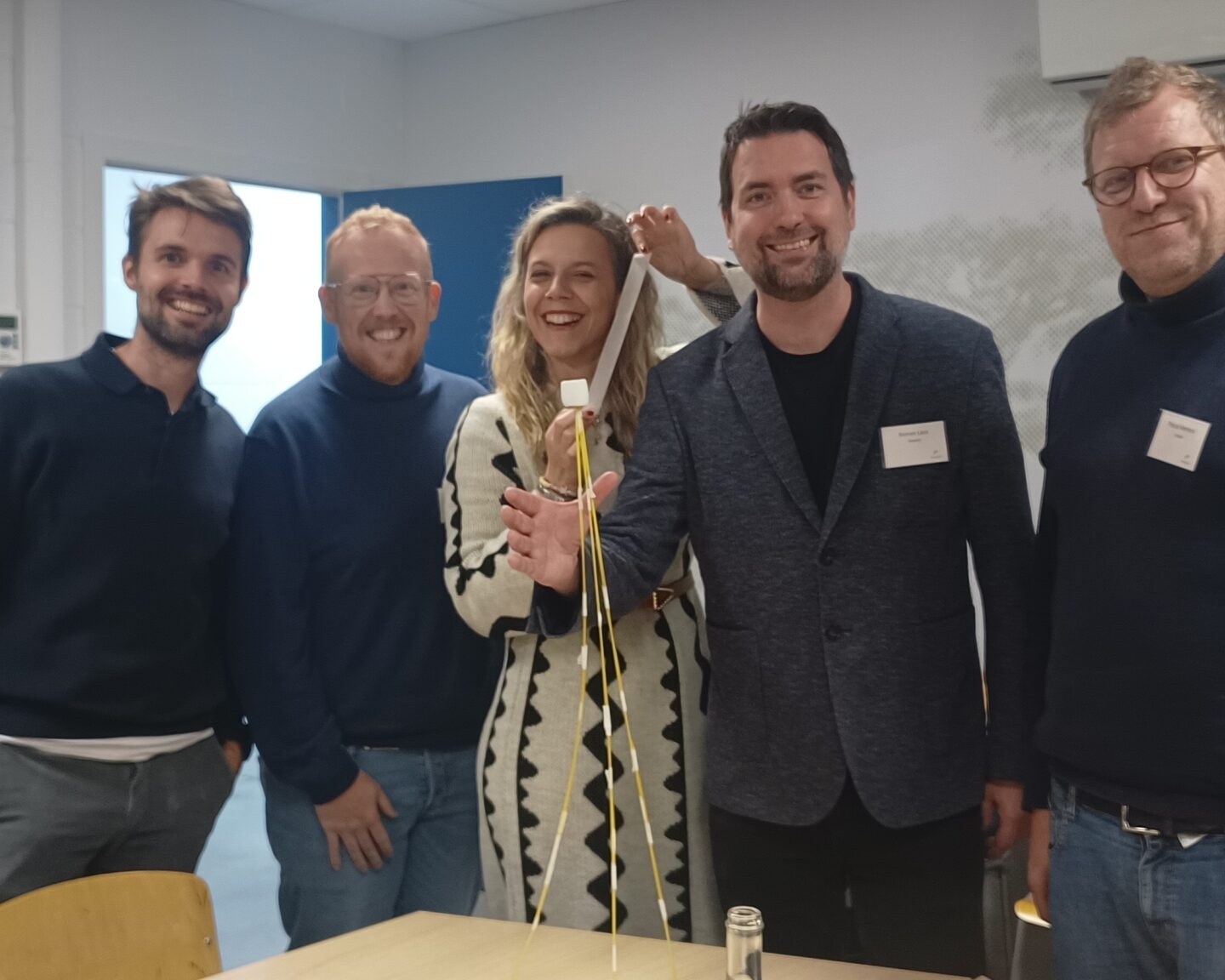
Networking with cohort six
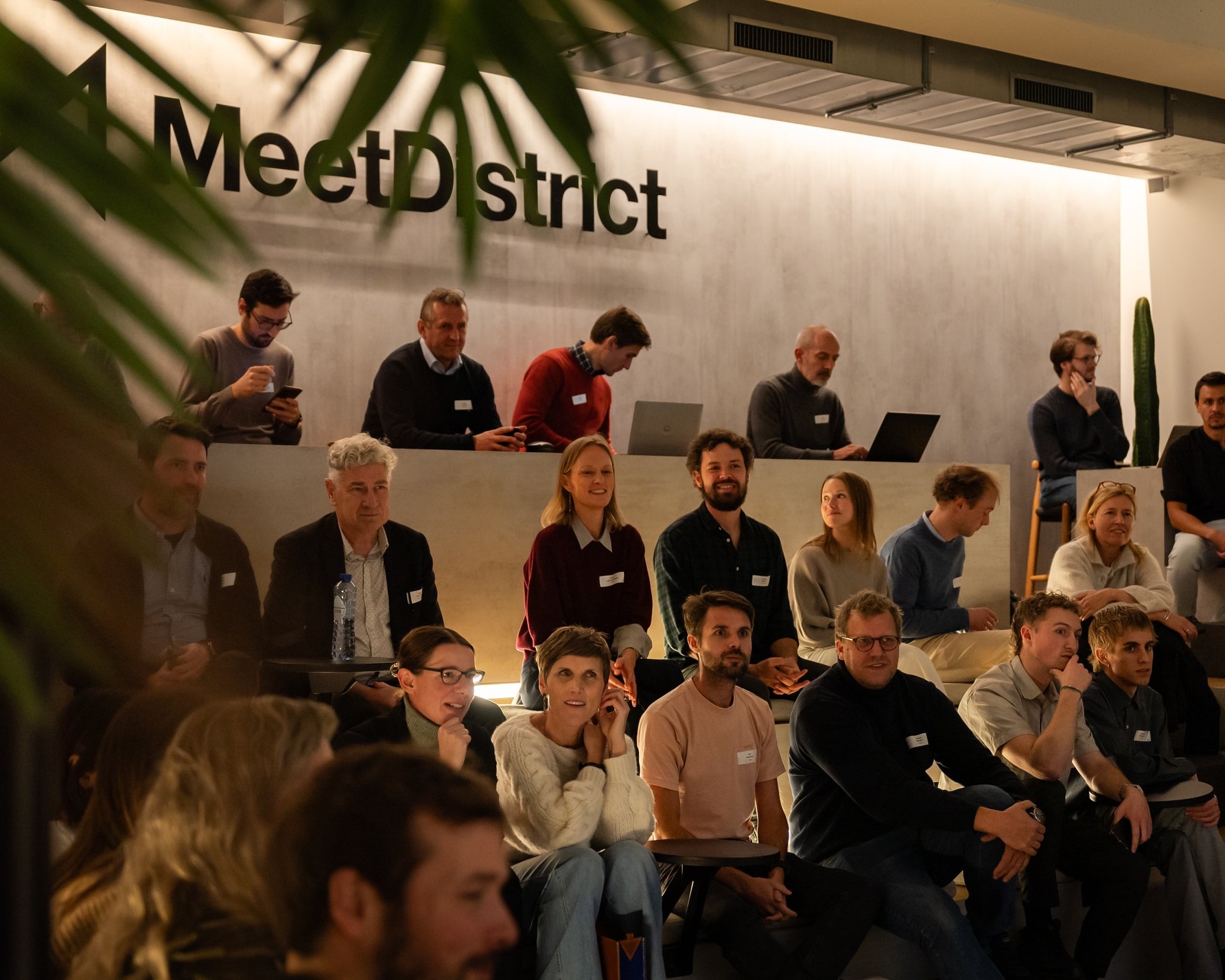
B’ZEOS celebrates seed round milestone
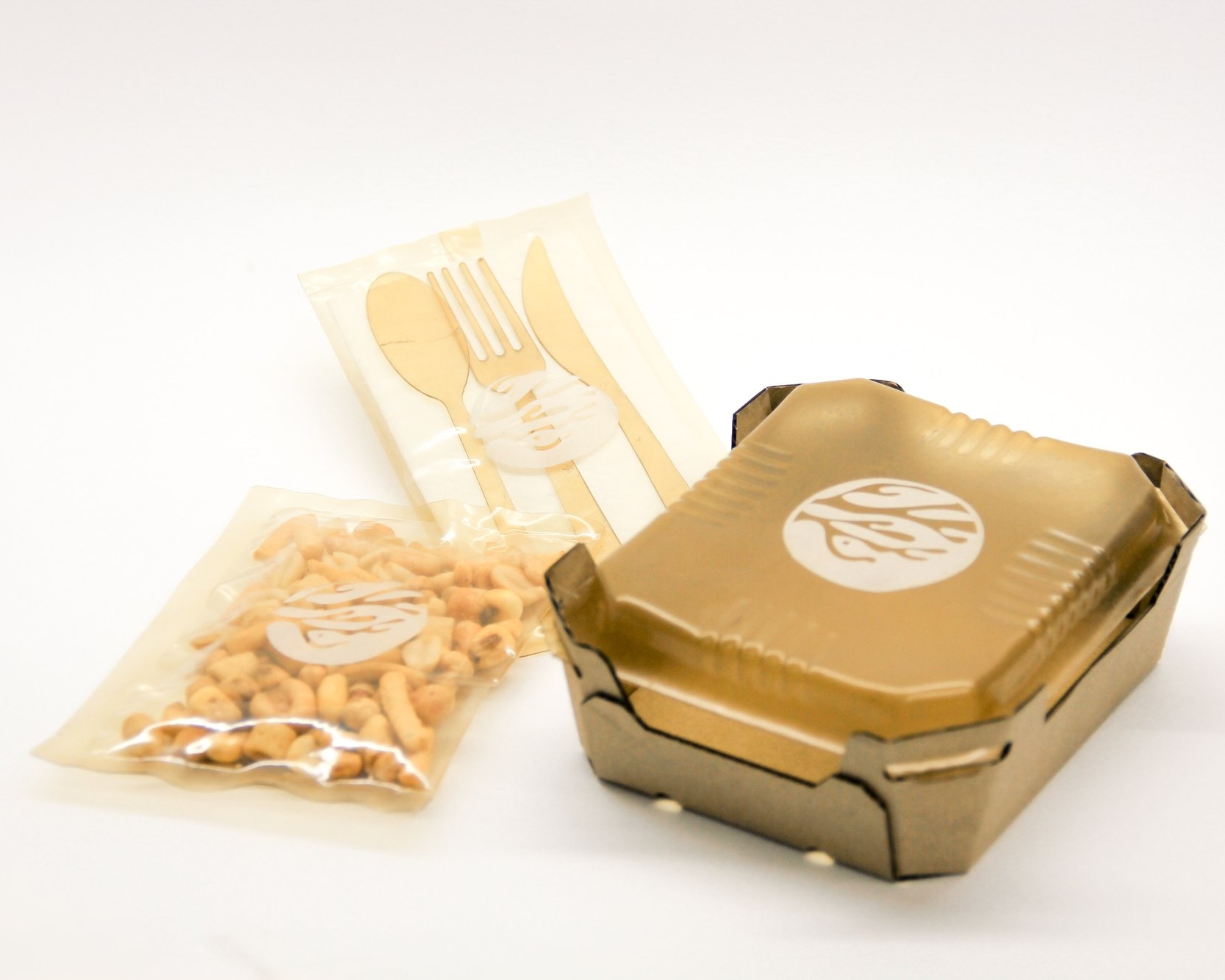
Tackling food waste at its source
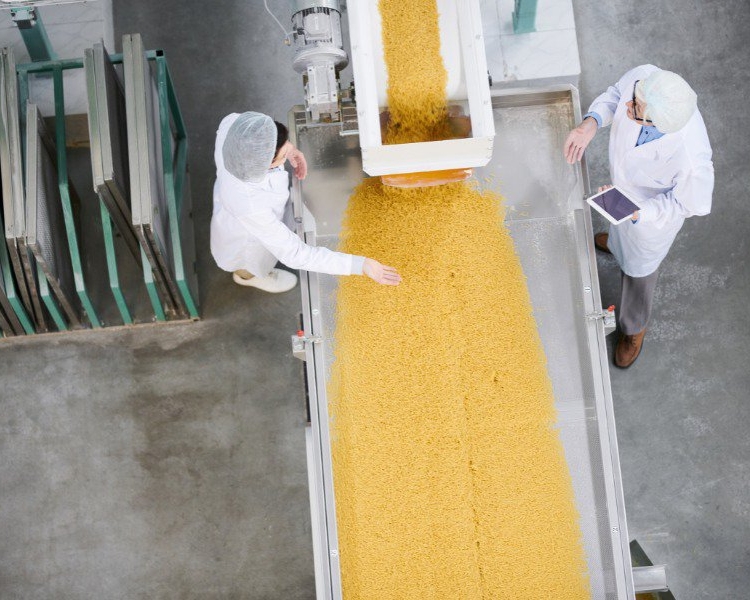
The value of good mentors

Meet our Spring ‘24 cohort

His son’s allergy turned this father into a founder
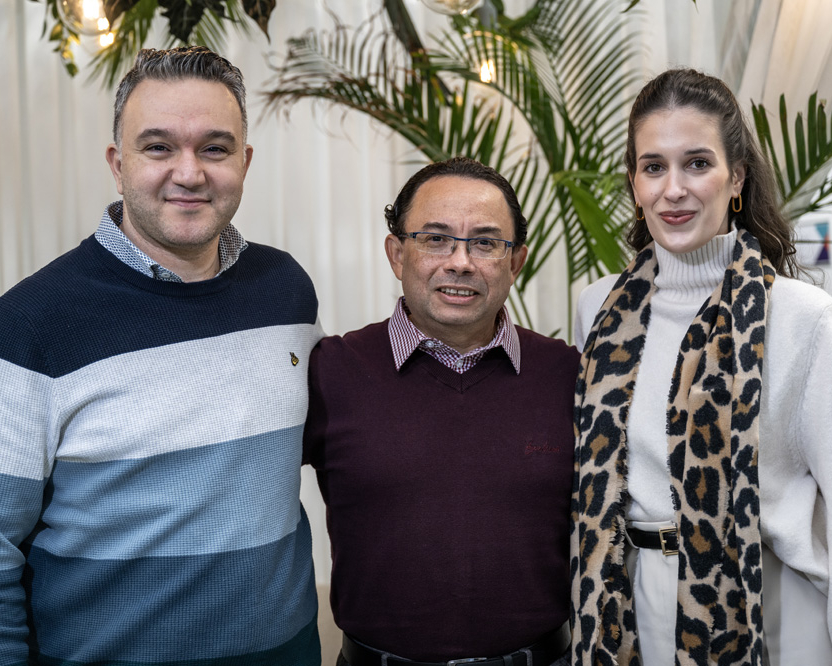
FlyBlast: on a mission to solve meat
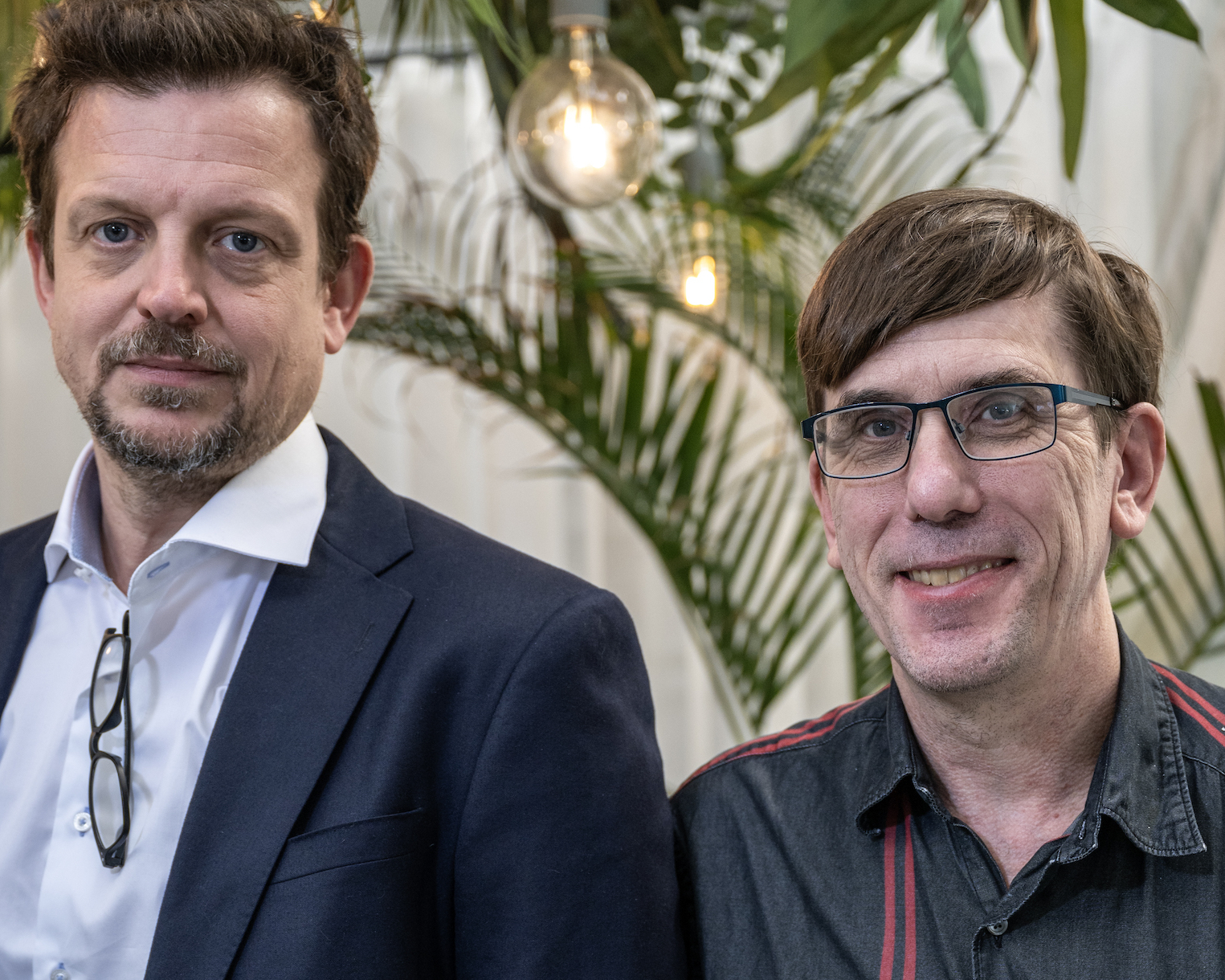
Probitat interview
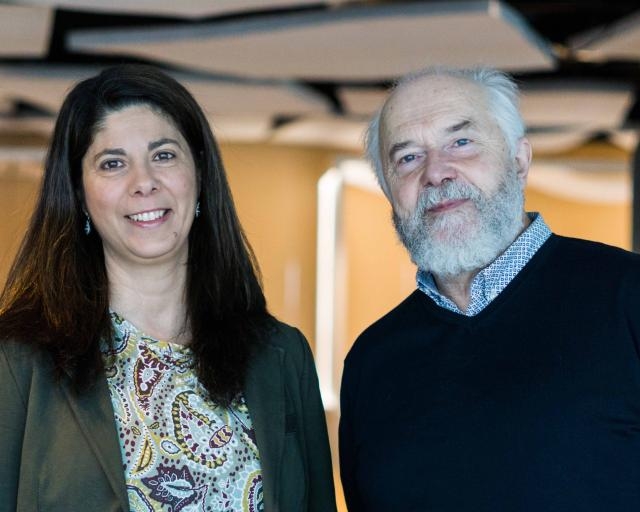
B’ZEOS: sustainable packaging made of seaweed
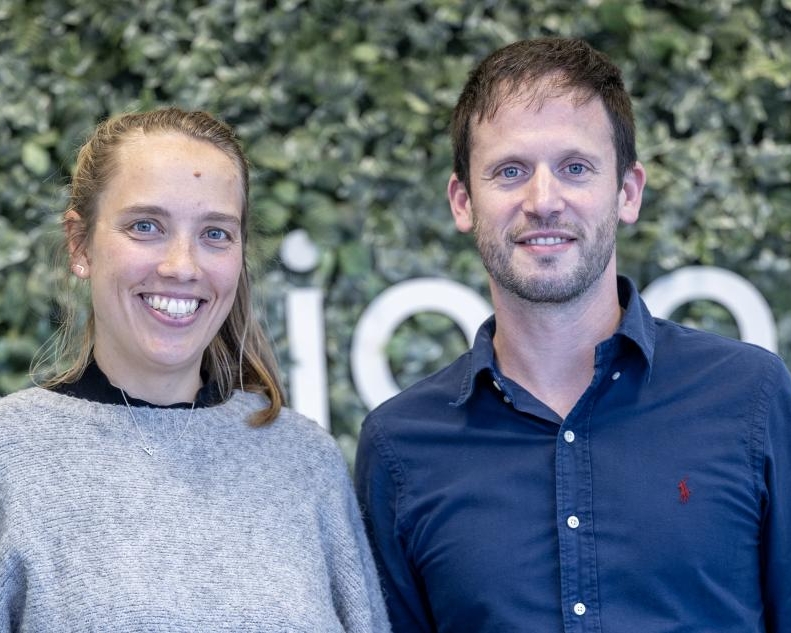
Elogium: Poultry probiotics for safer food
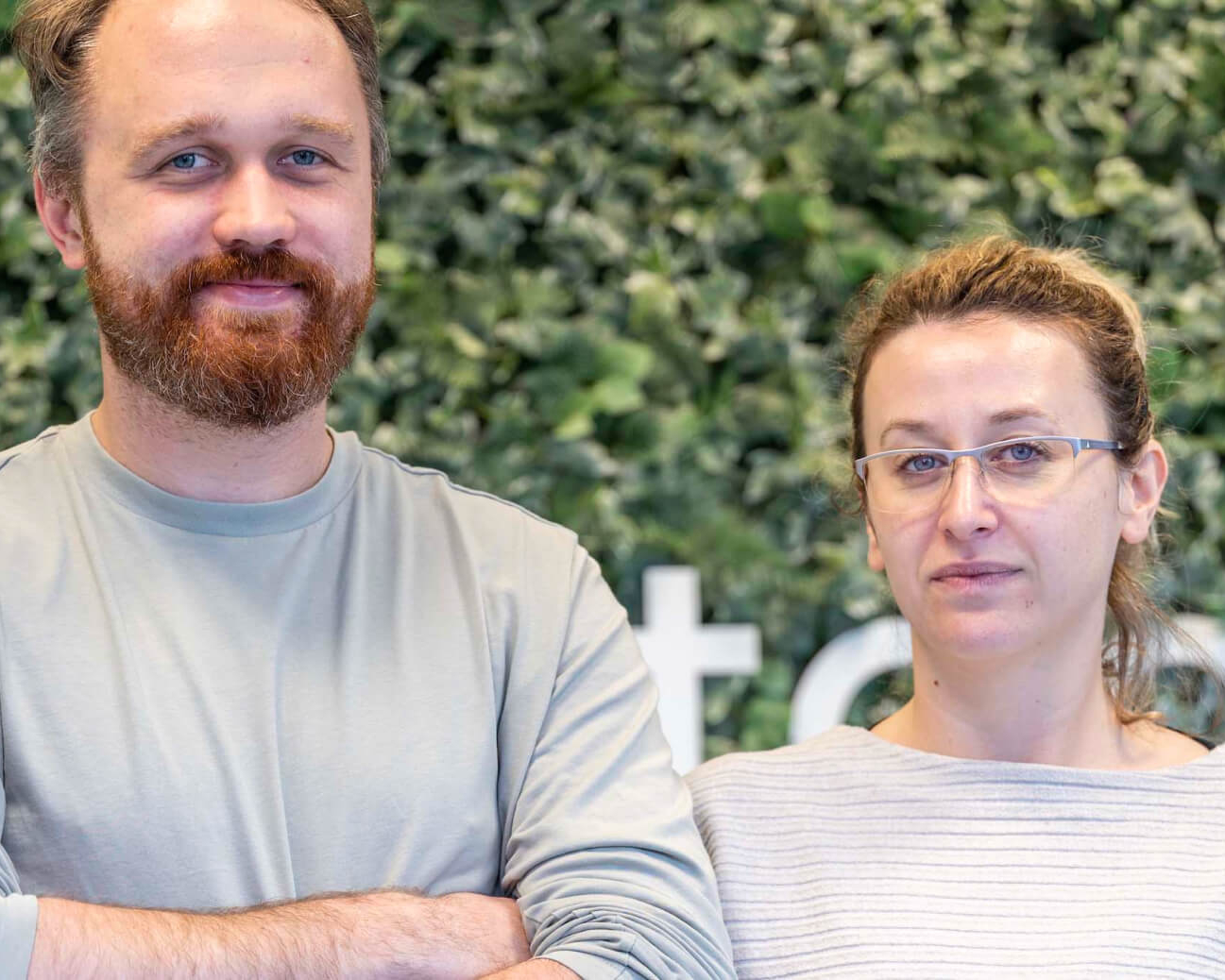
Launch of Biotope ventures fund
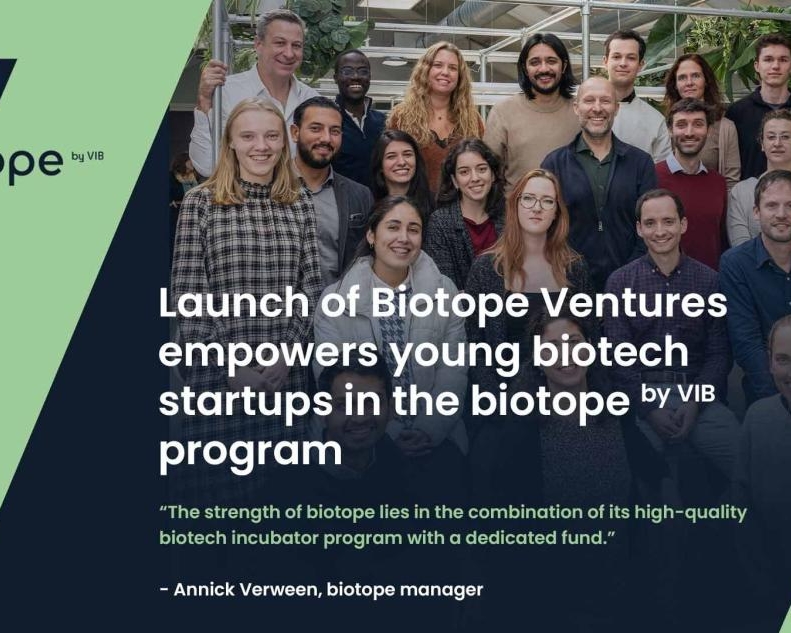
Bolder Foods: non-dairy cheese for a better world
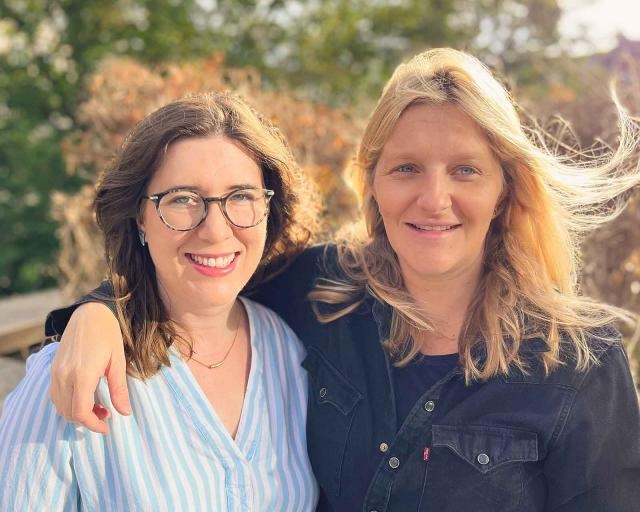
BioVox article

Have you got what it takes?
- Pressure-test your biotech with expert feedback
- Align your team and sharpen your strategy
- Turn your startup into an investment-ready business
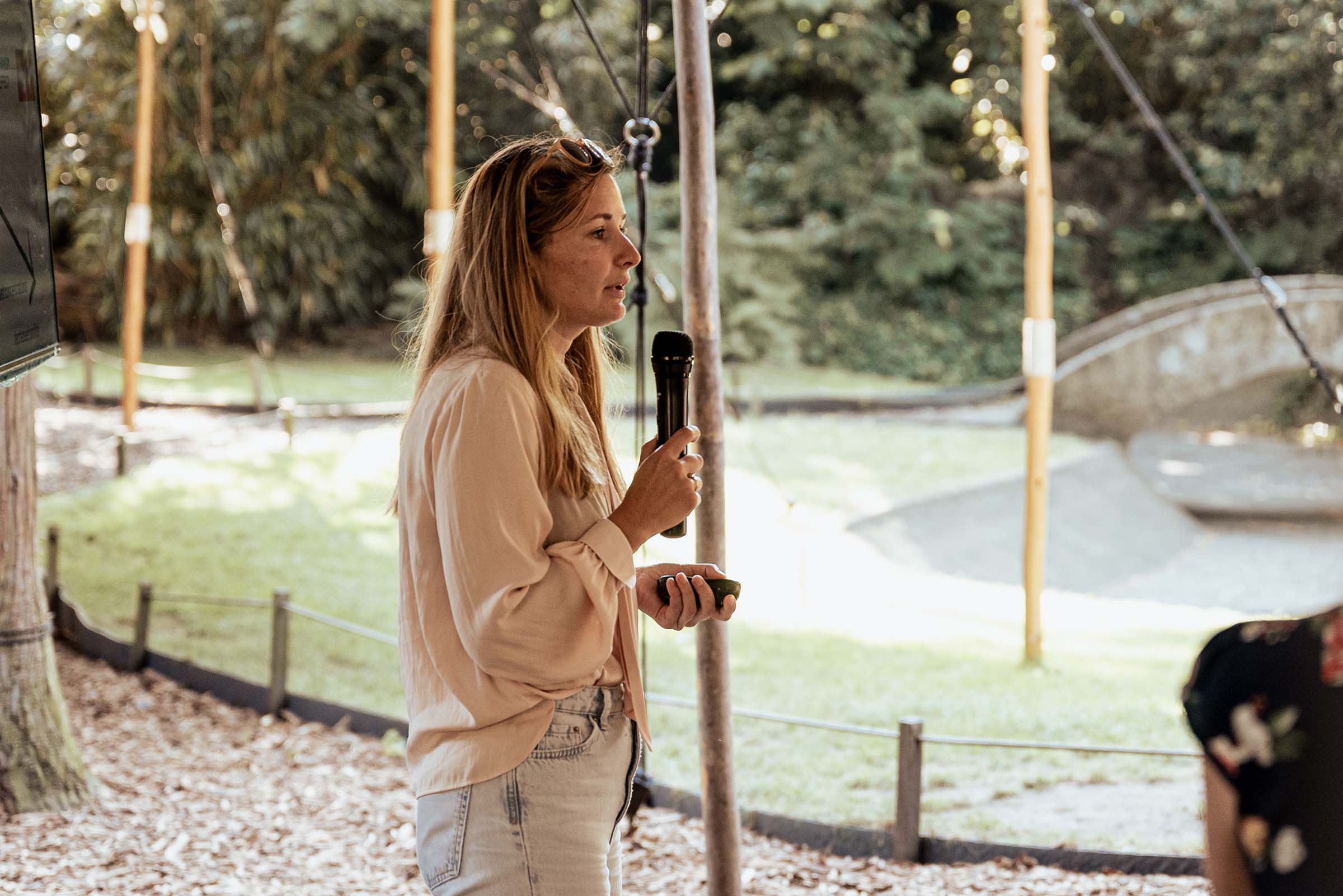